
What Are The Differences Between The XA100 & F135 Fighter Jet Engine?
History of the F135 Jet Engine
The Pratt & Whitney F135 Turbofan Jet Engine became the U.S. Air Force’s jet engine of choice for the F-35 Joint Strike Fighter Program in 2001; it went into low-rate initial production (LRIP) in 2009. The F135 was a derivative of the P&W F119 engine used on the F-22 Raptor.
In 1994 the Pentagon’s Joint Strike Fighter Program (JSF) issued a Request for Information (RFI) to begin the selection process for a prime defense contractor for what would eventually become the F-35 Lightning II.
In 1995, Boeing, Lockheed-Martin, McDonnell-Douglas, Northrop-Grumman, and British Aerospace submitted RFIs. All five contractors were asked to indicate which jet engine manufacturer’s prototype powerplant would best suit their vision of a JSF.
Photo: Congressional Research Service
Four of the prime contractors selected the Pratt & Whitney F135 engine; only one company selected General Electric’s proposed powerplant. In 1997, the JSF Program Office down-selected Boeing and Lockheed-Martin; both had chosen the P&W powerplant – the F135 precursor.
The truth be known, any companies other than Lockheed-Martin and Pratt & Whitney, had a steep mountain to climb. Several years earlier DARPA (Defense Advanced Research Project Agency) had issued a classified R&D contract to Lockheed-Martin’s Skunk Works in Palmdale, CA.
DARPA asked the Skunk Works to figure out a path forward for a new STOVL jet that would replace the Marine Corps’ aging fleet of AV-8B Harrier II jump jets. The Skunk Works chose P&W to partner with them on the DARPA project.
DARPA’s technology breadth is staggering. An example is Northrop Grumman’s Manta Ray sub-surface UAV Program.
Photo: Lt. j.g. Drew Verbis l Naval Base Ventura County l DARPA
A year or two later, the JSF Program came to life, and they were looking for a fighter jet to meet USAF needs, able to operate from an aircraft carrier for the Navy, and also be the Marine Corps’ new STOVL fighter. Needless to say, both Lockheed-Martin and Pratt & Whitney were very interested in the JSF.
The DARPA project gave a head start for the two long-serving defense contractors – Pratt & Whitney and Lockheed Martin.
Circling back to JSF’s 1997 down-selection decision, each contractor was asked to build two CDP (concept demonstrator prototype) aircraft. Lockheed Martin’s CDP was designated the X-35, and Boeing’s was the X-32 (shown here).
Photo: Edwards AFB l U.S. Air Force
After a multiyear flight test program on both planes simultaneously, Lockheed-Martin and Pratt & Whitney won the deal in 2001. In keeping with Pentagon policy, the aircraft and jet engines were contracted separately. P&W would make the F135 turbofan engine, sell it to the JSF, and then ship it to Lockheed-Martin as GSE (government-supplied equipment).
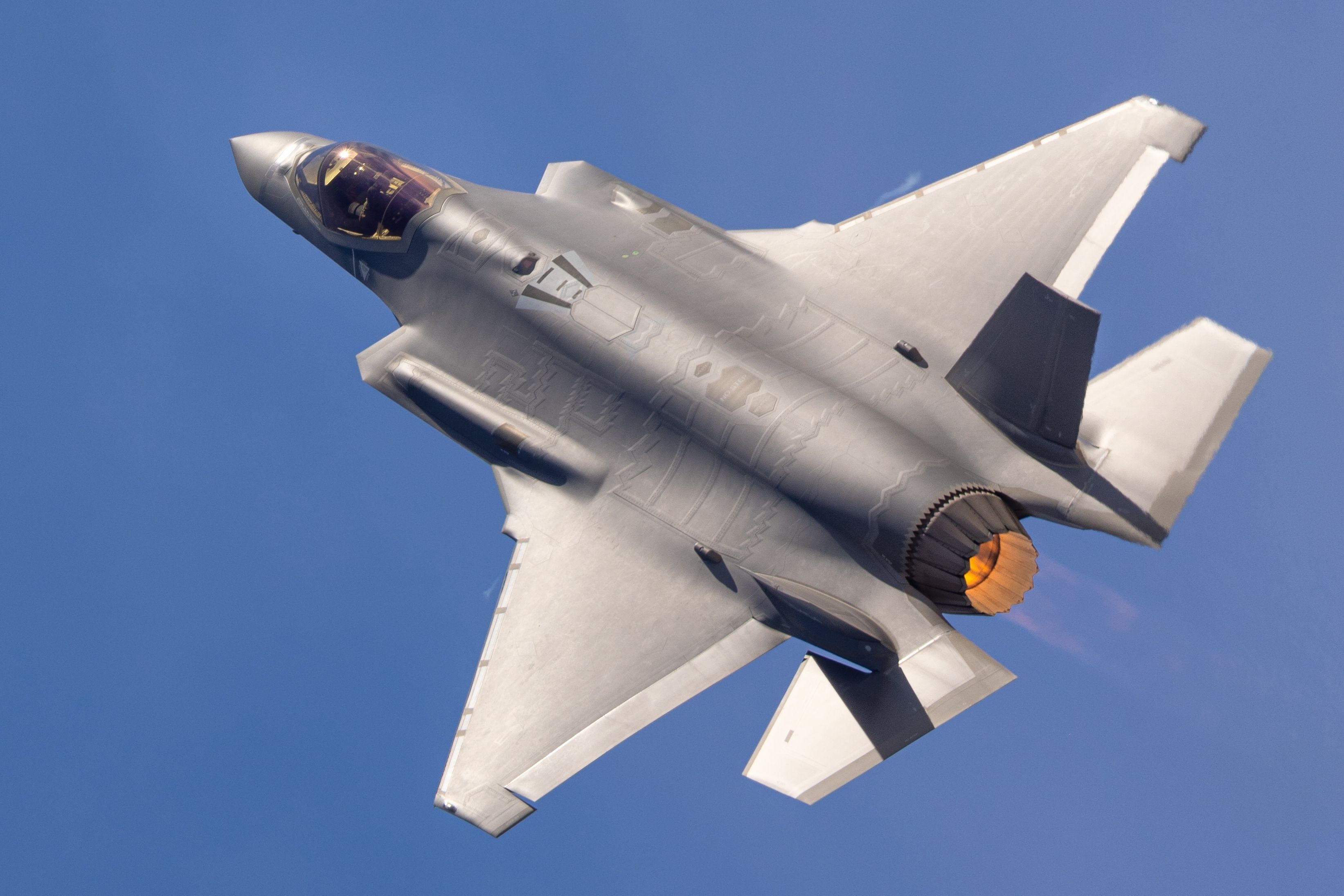
Related
F-135 Block 4 Advances As RTX Pratt & Whitney Completes Engine Core Upgrade Preliminary Design Review
The first deliveries of the ECU are planned for 2029.
The Pentagon’s conundrum in dealing with two jet engine manufacturers
There are other jet engine manufacturers in the world, but not for use aboard an American aircraft that is a critical national security asset – jet fighters. If the U.S. got into a multidomain shooting war like Vietnam, fighter jets would carry a huge load.
If the Pentagon had only one American, high-performance jet engine manufacturer to support its fleet of fighter jets, including a major manufacturing ramp-up, it would be a serious supply chain failure.
Even if the Pentagon only had enough work for one fighter jet engine manufacturer during peacetime, it would be a serious national security risk to not have production capacity that could be ramped up quickly. America must have both General Electric and Pratt & Whitney producing fighter jet engines.
The Pentagon fighter jet program community has to manage a delicate balancing act to keep both engine manufacturers employed and profitable. Pentagon program managers have learned in the past 60 years that they are asking for a lot of trouble if they try to simultaneously buy jet engines from G.E. and P&W for a new fighter jet under development.
It is complicated to get just one engine OEM fully integrated into a new aircraft, let alone two of them. The Pentagon tries to allow each company to be the prime engine OEM on new aircraft programs.
If a given fighter jet, like the F-16 for example, stays in production long enough, Pentagon program managers will engage the non-prime engine maker to qualify their product for use. The two engines are not interchangeable plug ‘n play replacements.
Photo: A1C Connor Taggert l 177th Fighter Wing l N.J. Air National Guard: U.S. Air Force
The F-16 has a G.E. version and a P&W version. The Air Force has Lockheed-Martin build the F-16 in “production blocks,” to distinguish which batch of planes has one OEM’s engine vs the other engine maker.
Here is an example: When the aircraft went through an upgrade in the mid-1980s, it was significant enough that they rolled the revision from F-16A single-seaters, and F-16B two-seaters, to the F-16C and F-16D. These aircraft were the first F-16s to utilize both the original G.E. F110 engine and the P&W F100 engine.
Photo: Petty Officer 2nd Class Isaiah Goessl l U.S. Navy
Since the two engines are not physically or electronically interchangeable, the F-16C/Ds have Block 50s with G.E. and Block 52 with P&W.
This scenario has been on the minds of the JSF program office and General Electric for over two decades. There have been too many open action items that left no bandwidth for the program office or Lockheed Martin to qualify G.E.’s alternative engine for the F-35.
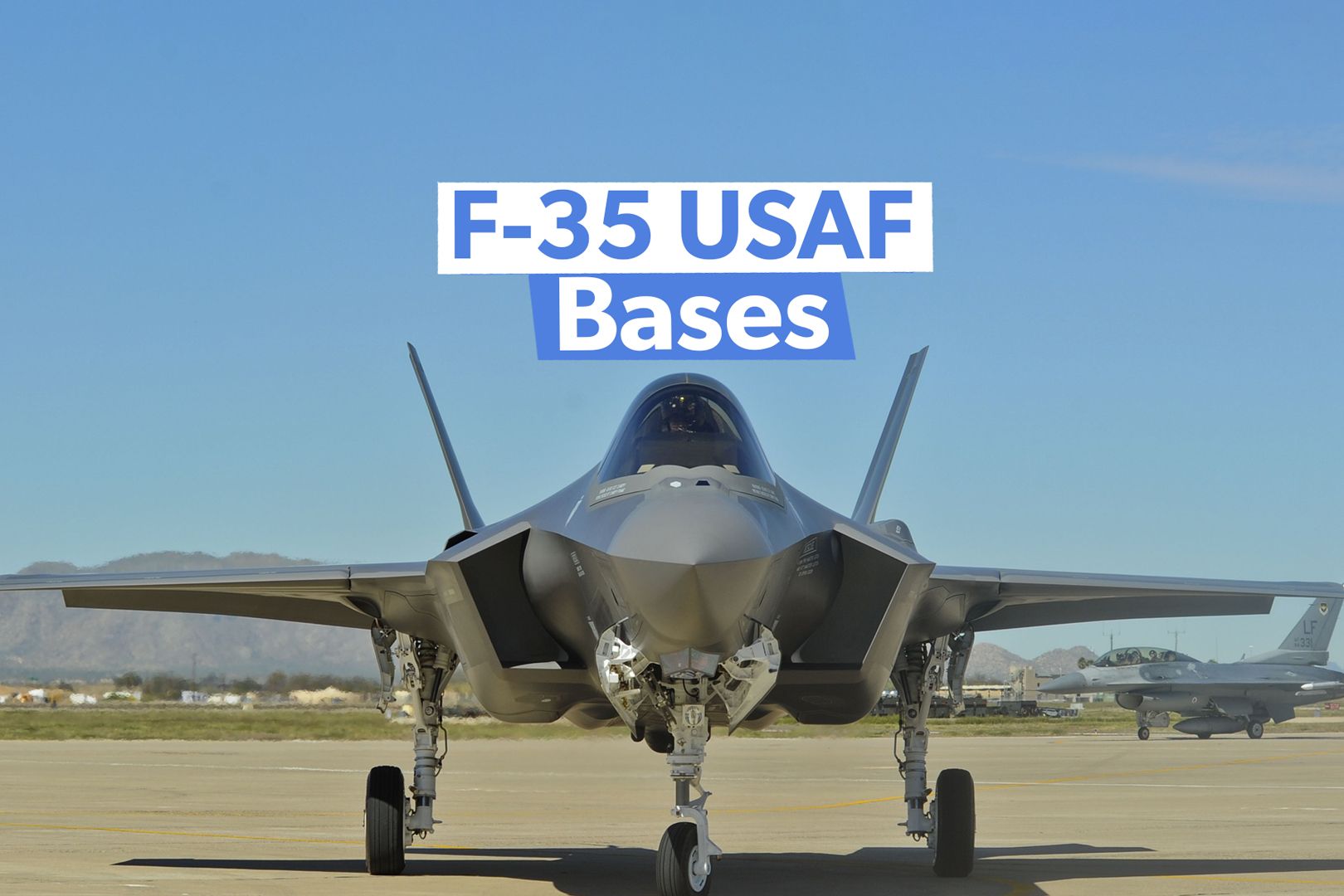
Related
What US Air Force Bases Have F-35s?
Ten air force bases are listed as bases for the USAF F-35A, although they can operate from many more bases.
General Electric proposes a very different type of jet engine
To G.E.’s credit, they proposed a type of turbofan engine for the F-35 that was more than a “me too” just to capture some of P&W’s F135 engine sales. They came up with the XA100 engine; which uses “Adaptive Versatile Engine Technology” (AVET). AVET has been studied extensively in the past 20 years, but not to the level of serious consideration in any current fighter jets.
Jet engine technology from World War II through the mid-1960s was based on the turbojet. Turbojets were inefficient, underpowered gas guzzlers. This is why large aircraft back in the day, like the Boeing B-52, had eight engines.
The frontline fighter jet in the 1960s was the McDonnell F-4 Phantom II. Its two G.E. J79 afterburning turbojets could propel the plane up to Mach 2.2. If the pilot stayed at that airspeed, the fuel tanks would be bone-dry in eight minutes!
Photo: Tech. Sgt. Emili Koonce l 48th Fighter l DVIDS
That sort of flight profile is justifiable in active air combat, but not otherwise. Large aircraft, such as bombers, cargo planes, and airliners, do not have a flight envelope that needs that sort of “instant speed.”
Sub-sonic aircraft needed an alternative to the turbojet, and the turbofan jet engine was born. In a turbojet, all of the air scooped-up by the engine intake is funneled through the engine’s core (combustion chamber). Any air going through the jet’s core is mixed with fuel and combusts.
A turbojet is considered a low-bypass engine; very little air bypasses the core. A turbofan, on the other hand, has a disproportionately large fan in front of the intake on large, civilian jets. The fan bypasses 80% to 95% of the air around the core.
Turbofans are considered high bypass engines and are known for their fuel efficiency, quietness, and far more power than any of their turbojet predecessors.
It is amazing that when Boeing first flew the 747 jumbo jet in 1969, it took four turbojet engines to meet the performance requirements and an adequate safety margin if an engine went out.
Photo: Markus Mainka l Shutterstock
Fast-forward 25 years to Boeing’s introduction of the 777 widebody jet with only two turbofan engines, but it could fly safely on just one!
It would seem like turbofans were the answer for all jet aircraft, except for one major problem: Turbofans have most of their intake air bypassing the core combustion chamber.
If the plane needs to accelerate rapidly using the throttle, more fuel is injected into the combustion chamber causing greater thrust. The airspeed will increase, but without additional air funneling into the combustion chamber, it will not accelerate rapidly.
Photo: Glenn Research Center l NASA
Sluggish acceleration might be okay for an airliner, but not a fighter jet. To attain maximum performance, fighter jets retained their low bypass engine, but are now turbofans to take advantage of benefits other than acceleration.
The F-35’s P&W F135 is a high-powered, sophisticated powerplant, but it is still a low-bypass engine. The F135 is a turbofan engine, but it is still not a very efficient engine. But, when it comes to what the Joint Strike Fighter is supposed to do, the Pentagon is not going to sacrifice performance for better gas mileage!
The genesis of the General Electric experimental XA100 engine
Putting it simply, the Air Force and Navy’s fighter jet community needed a hybrid jet engine that offered the benefits of both low-bypass turbojets and high-bypass turbofans. To that end,
the Air Force issued R&D contracts in 2007 to G.E. and Rolls-Royce on the Adaptive Versatile Engine Technology (ADVENT) program.
ADVENT continued with several sub-level projects for the next 10 years. Eventually, Pratt & Whitney would also join the ADVENT program. For the first few years, the Air Force managed the program without targeting any specific aircraft.
This non-specificity status finally coalesced in 2016 as a new engine for the 6th generation fighter under the Next Generation Air Dominance (NGAD) program. G.E.’s XA100 is an adaptive cycle engine focused on the NGAD program.
By 2018, the ADVENT program added the F-35 reengining initiative. G.E. continued with the XA100’s development. They had also been working on qualifying their F136 low bypass ratio turbofan for competing against the P&W F135 engine.
The R&D results from ADVENT were encouraging. It was so encouraging that the Air Force Life Cycle Management Center (AFLCMC) informed G.E. to divert resources from the NGAD program to qualify the XA100 for the F-35. P&W was assigned XA101 for developing their version of an adaptive versatile jet engine.
G.E. finished their XA100 testing program in 2021. The USAF life cycle engineers wanted to issue a contract to G.E. to put the engine into production, with usage on the F-35A and C models, starting in 2027.
Things changed in 2023 when the USAF set aside integrating the G.E. XA100 with the F-35 fighter. Two issues surfaced: the high conversion cost and concern over the XA100’s engineering integration to the “B” and “C” F-35s. The XA100 still has the inside track for the NGAD Program.
The USAF decision to hold off on XA100 usage became more palatable to the Air Force when they finished testing P&W’s Engine Core Upgrade (ECU) for their F-135 turbofan engine. Introduction to the F-35 fleet is scheduled for 2029.
G.E.’s original interest was getting their F136 equivalent to P&W’s F135 engine qualified for the F-35. They have ended up with no revenue-generating contracts, and the XA100 ADVENT engine for the 6th generation NGAD fighter is unlikely to generate any profits until after 2030.
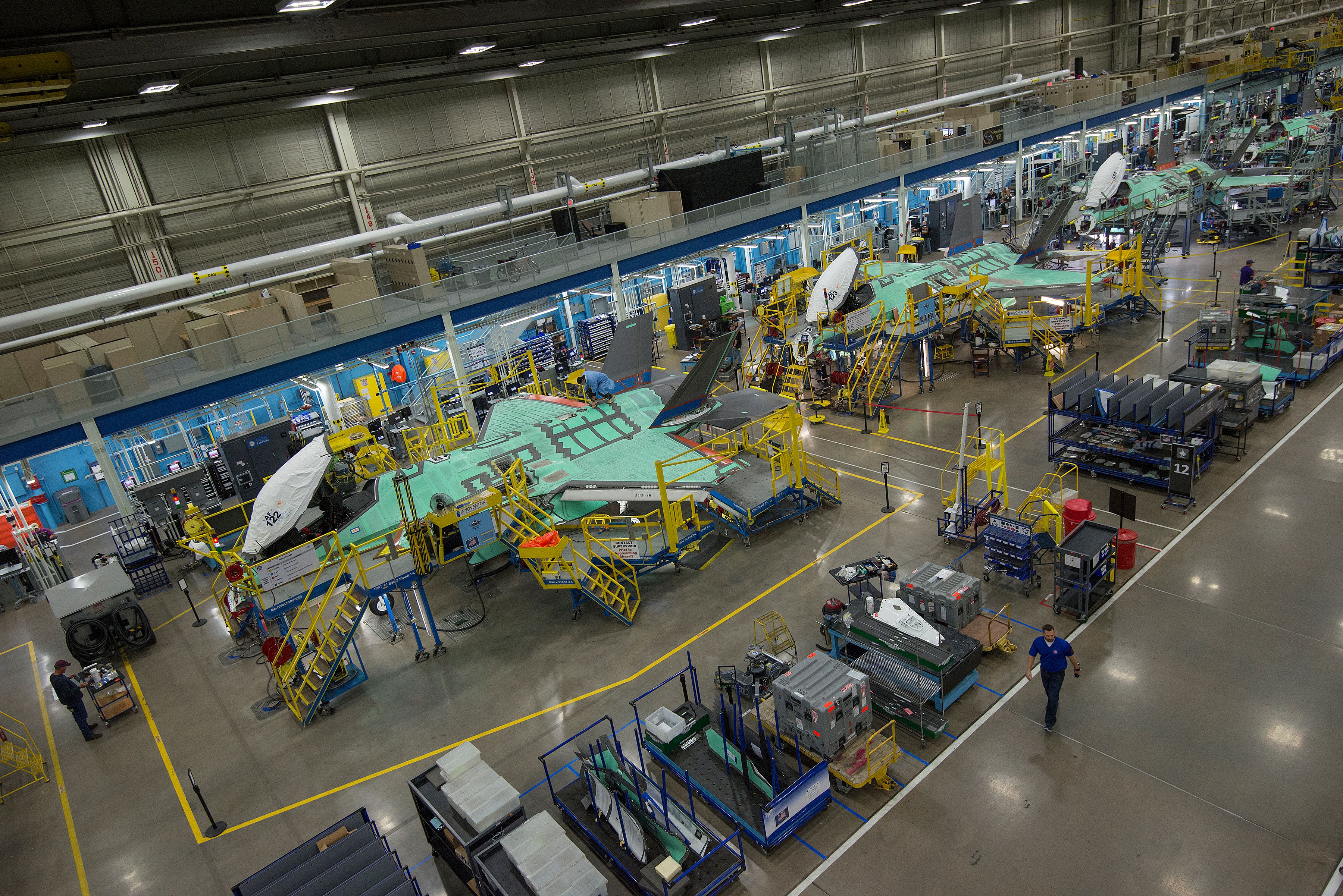
Related
Lockheed Martin On Track To Deliver 100 F-35s To The US Military This Year
Lockheed is set to meet its upper target for F-35 deliveries in 2024 and appears set to exceed 2023 deliveries.
Spotlighting the main differences between the XA100 and F135
- The most significant difference is the P&W F135 is strictly a low-bypass turbofan engine. G.E. labels the XA100 as a variable or adaptive cycle engine. Rather than the XA100 designed as a high bypass turbofan or low bypass turbofan, it is a hybrid engine that has been designed to function well in multiple flight profiles above Mach one, high sub-Mach one (transonic), and subsonic (0.3 Mach to .75 Mach). The subsonic flight would dictate the XA100 operating as a high bypass turbofan. Transonic speeds of .7 to .95 Mach dictates an engine mode of partial low bypass turbofan and partial high bypass turbofan. Supersonic would use the XA100 as a pure, low-bypass turbofan in afterburner.
- The same flight envelope using a G.E. XA100 adaptive cycle turbofan engine vs the P&W F135 low bypass turbofan, the plane had a 30% increase in range.
- The XA100 improved acceleration by 20%.
- The XA100’s ability to transfer from a high-performance, low-bypass turbofan, to a high-bypass turbofan improves fuel efficiency by 25%.
- Low bypass jet engines, whether it is turbojet or turbofan, do not manage their thermal profile very well; this is the situation with the F135. The engine is either not running hot enough, or it is running too hot. The XA100’s thermal profile is better controlled by 200% Excessive heat cycling causes component failures, reducing the MTBF.
- Modest flight testing has been done on the XA100, but not onboard an F-35. The problem is the large differences in physical attributes between the F135 and XA100. The F135 weighs about 4,000 lbs, and the XA100 weighs 6,400 lbs. The F135 is not quite four feet in diameter, and the XA-100 is six feet wide. Lastly, the XA100 is 20 feet long, but the F135 is two feet shorter.
- My engineering background tells me that adapting the XA100 to the F-35 Lightning II would be very difficult. It would be better to do a clean sheet design, like NGAD, than to integrate the new engine. USAF cost analysts estimate the XA100 integration costs for the F-35 would be double what it costs to integrate the F135 onboard the F-35.
- P&W has been successful with their F135 Engine Core Upgrade (ECU), but the Congressional Research Service, Government Accountability Office, and several nonprofits, like Citizens Against Government Waste, have been publishing white papers and reports about the risk of spending a lot of money on F-35/XA100 integration, I doubt the Elon Musk/Vivek Ramaswamy duo would sign off on spending a billion dollars for it.